速度反饋機(jī)制的收斂性同網(wǎng)格疏密程度,時(shí)間步長,試算初速度等相關(guān)。它在程序中實(shí)現(xiàn)的流程如圖3-14所示。
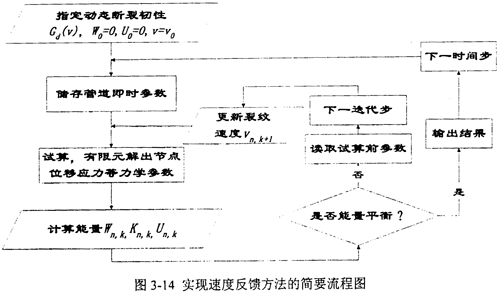
裂紋體的殘余動(dòng)能并不能全部用于驅(qū)動(dòng)裂紋擴(kuò)展,因?yàn)橄喈?dāng)一部分動(dòng)能包含在裂紡頂端后面較遠(yuǎn)的區(qū)域內(nèi)。Hahn(1973)對(duì)雙懸臂梁試樣的測(cè)試表明,約有85%的動(dòng)能消耗于裂紋驅(qū)動(dòng)能。修正后的(3-27)可以表示為:
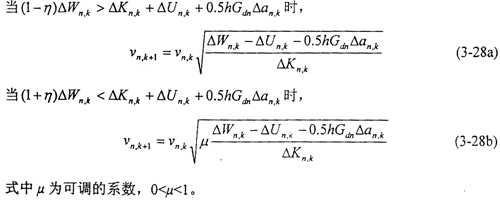
至此,韌性減速機(jī)理已經(jīng)基本建立。但(3-26)式中表示動(dòng)態(tài)斷裂韌性的關(guān)鍵量Gd的確定方法尚未解決。下面-小節(jié)我們將就此展開討論。
3.4.3 小試樣沖擊實(shí)驗(yàn)與Gd的關(guān)系
工程上廣泛使用小試件沖擊實(shí)驗(yàn)的辦法測(cè)定管道材料的動(dòng)態(tài)斷裂韌性,具體測(cè)試手段與結(jié)果在第四章另有詳述。
本小節(jié)的目的是通過小試樣沖擊實(shí)驗(yàn)的設(shè)計(jì)參數(shù)和測(cè)得的吸收功,給出韌性減速機(jī)理中代表動(dòng)態(tài)斷裂韌性的關(guān)鍵量Gd的基本表達(dá)。
2.1.4節(jié)已經(jīng)提到,動(dòng)態(tài)斷裂韌性Gd除與材料的性質(zhì)密切相關(guān)外,還與環(huán)境溫度,應(yīng)力狀態(tài),試件厚度,特別是斷裂速度關(guān)系密切。
因小試件沖擊實(shí)驗(yàn)與管道全尺寸裂紋擴(kuò)展的相似性,忽略應(yīng)力狀態(tài)對(duì)斷裂韌性的影響。設(shè)小試件沖擊實(shí)驗(yàn)中的特定參數(shù)為試件厚度h0,沖擊速度v0,實(shí)驗(yàn)環(huán)境溫度T0,韌帶寬度即裂紋擴(kuò)展長度a0,測(cè)到的外力吸收功為W0。
由忽略表面能的(3-21)式,小試件裂紋擴(kuò)展中的動(dòng)態(tài)斷裂韌性Gd0。可表示為:

式中λ為材料的塑性功率,v為瞬時(shí)擴(kuò)展速率,a為瞬時(shí)裂紋長度,O<a<a0。注意這里裂紋每擴(kuò)展da,新增裂紋面面積為2hda。
考慮裂紋擴(kuò)展過程中的某微小時(shí)間增量dt,對(duì)小試樣沖擊的實(shí)驗(yàn)過程應(yīng)用能量平衡方程(3-22)式并對(duì)裂紋擴(kuò)展全過程在時(shí)間上進(jìn)行積分:

式中△W、△U、△K分別為裂紋擴(kuò)展過程中試件消耗的外力功、應(yīng)變能增量和動(dòng)能增量,WC為裂紋開裂過程消耗的起裂功。對(duì)于高韌性鋼,△U、△K可忽略。
因小試件試樣斷裂時(shí)間很短,可假定起裂后的斷裂速度始終等同于擺錘的沖擊速度v0。另外考慮在試樣尾部因裂紋前端發(fā)生塑性形變的范圍變短,Gd會(huì)相應(yīng)有所損失,令這-部分損失的能量為P(h0,T0,v0),則:

式(3-31)可以作為確定式(3-26)至式(3-28)中Gd(h,T,v)的依據(jù)。
3.4.4 待定參數(shù)的確定
式(3-31 )留下了We和P兩個(gè)參數(shù)有待確定。根據(jù)其物理意義,可以通過預(yù)制裂紋、脆化缺口等方法消除We的影響。雙試件實(shí)驗(yàn)更可以達(dá)到雙重目的,通過兩次不同韌帶寬度a1和a2的試件(其余條件完全相同)的實(shí)測(cè)吸收功W1,W2之差,可以直接得到Gd0:

因?yàn)橛绊戫g性的參數(shù)比較復(fù)雜,最可靠的做法是采用和真實(shí)管道同樣的壁厚,在一系列溫度和沖擊速度下用雙試件法測(cè)定斷裂韌性,以備計(jì)算采用。
3.5 基于韌性減速機(jī)理的算例分析
韌性減速機(jī)理應(yīng)用于有限元計(jì)算后,可以方便地隨意指定計(jì)算區(qū)域內(nèi)的管道裂紋的初速度v0,通過第四章的小試件方法測(cè)到的動(dòng)態(tài)斷裂韌性Gd,模擬整個(gè)管道包括速度變化的曲線在內(nèi)的真實(shí)開裂情況。
本文通過上述方法,對(duì)圖3-9至圖3-12中的全尺寸實(shí)測(cè)斷裂速度曲線結(jié)果進(jìn)行了校核,得到了比較吻合的結(jié)果�,F(xiàn)以聯(lián)盟管道第一次實(shí)驗(yàn)IE段為例,設(shè)定擴(kuò)展的初速度為330m/s,速度變化的計(jì)算值同實(shí)驗(yàn)對(duì)比如圖3-15所示:
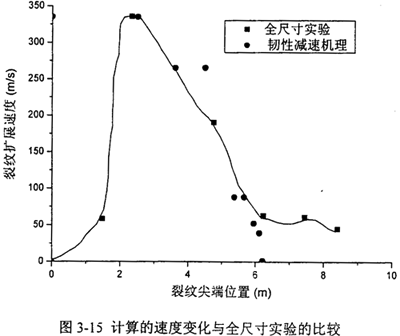
通過大量的測(cè)算與歸納,得到吻合較好時(shí)的Gd與CVN能量的關(guān)系:
Gd=1.3cKV=0.016CKV (3-33)
式中cKV和CKV分別是單位面積標(biāo)準(zhǔn)夏比沖擊韌性值和標(biāo)準(zhǔn)夏比沖擊功,cKV=CKV/(hoao),對(duì)于標(biāo)準(zhǔn)CVN試件,h0=10mm,a0=8mm。
另外,當(dāng)斷裂速度降至低于100m/s時(shí),要考慮偏隨速度的降低:
當(dāng)v<100m/s,Gd=o.8cKV+0.5cKV·v/100 (3-34)
直至止裂時(shí)Gd降為止裂韌性0.8cKV。
(3-33)和(3-34)式中的系數(shù)1.3和O.8的獲得方法為大量試算后取與全尺寸速度實(shí)測(cè)結(jié)果普遍吻合較好的值。
根據(jù)圖3-16中的MISES應(yīng)力分布可以判斷裂尖處的塑性區(qū)范圍。隨著裂紋擴(kuò)展過程中韌性導(dǎo)致的速度降低,塑性區(qū)的范圍逐漸縮小。
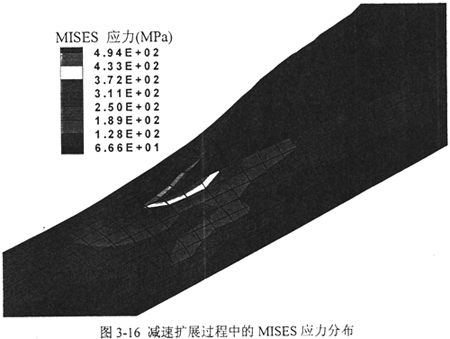
圖3-17和圖3-18是針對(duì)西氣東輸某特定設(shè)計(jì)參數(shù)的管線,應(yīng)用韌性減速機(jī)理計(jì)算時(shí)能量釋放率G和裂紋尖端張開角CTOA的變化。
隨著計(jì)算輸入韌性Gd導(dǎo)致的裂紋不斷減速,G和CTOA衰減幅度明顯,直至止裂。
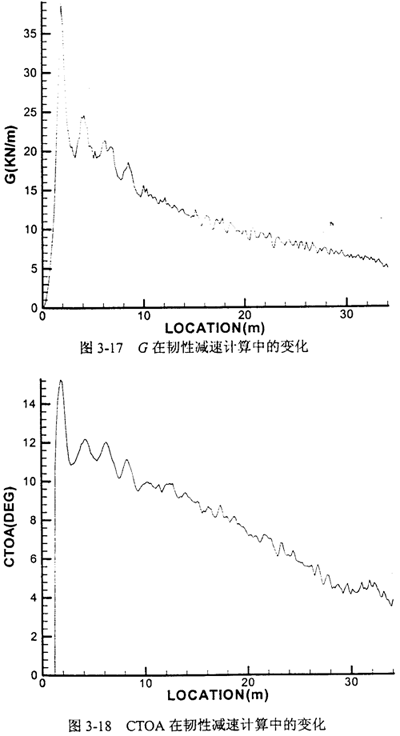
3.6 本章小結(jié)
全尺寸爆破實(shí)驗(yàn)中觀測(cè)到的速度變化表明,對(duì)于高韌性管線,由塑性功耗散引起的動(dòng)能衰減不可忽略。裂紋在低于預(yù)測(cè)斷裂韌性的均質(zhì)管道中也會(huì)發(fā)生明顯的減速現(xiàn)象,直至止裂。Maxey雙曲線法在預(yù)測(cè)高韌性鋼止裂韌性時(shí)發(fā)生的偏差是上述論述的有力旁證。
為此我們引入了依靠全尺寸實(shí)驗(yàn)指定裂紋擴(kuò)展速度變化的實(shí)測(cè)減速模型,將全尺寸實(shí)驗(yàn)的速度歷史通過參數(shù)分析應(yīng)用到待測(cè)管線。因影響裂紋擴(kuò)展速度的原因過于復(fù)雜,這種做法的可靠性不能保證。
本章的主要工作是通過流變斷裂學(xué)的基本理論,推導(dǎo)了對(duì)于瞬態(tài)裂紋擴(kuò)展,動(dòng)態(tài)斷裂韌性在整體能量平衡方程中所起的作用,并在有限元中構(gòu)造了迭代算法。表征材料韌性的參數(shù)Gd(v)通過小試樣實(shí)驗(yàn)確定,在計(jì)算中作為已知函數(shù)代入。
通過和真實(shí)裂紋擴(kuò)展曲線的對(duì)照,建立了通過夏比沖擊功估算Gd的經(jīng)驗(yàn)?zāi)P停?-33)和(3-34),并據(jù)此對(duì)特定參數(shù)的管道進(jìn)行了分析。
夏比沖擊和DWTT實(shí)驗(yàn)測(cè)試的是試樣斷裂的總能量�?偰芰堪ㄆ鹆涯�、裂紋擴(kuò)展能、塑性變形能和拋擲試樣的動(dòng)能。已有對(duì)DWTT試樣的研究認(rèn)為前兩部分能量占總能量的絕大部分。因而,本文認(rèn)為雙試件DWTT實(shí)驗(yàn)是最合適的小試件測(cè)定Gd(v)的手段。
但對(duì)于大多數(shù)工程情況,該實(shí)驗(yàn)條件難以被滿足。這就需要采用判定動(dòng)態(tài)斷裂韌性的一般方法,如CVN和DWTT,尤其是CVN。這是因?yàn)楣こ躺贤鶄溆懈鞣N溫度下的一系列夏比沖擊能量的數(shù)據(jù)。
在用全尺寸管道實(shí)驗(yàn)的數(shù)據(jù)作校對(duì)的時(shí)候,同樣會(huì)遇到類似的問題。一般情況下關(guān)于管道韌性的數(shù)據(jù)僅有CVN沖擊能量和DWTT吸收功,所以有必要對(duì)這兩種實(shí)驗(yàn)進(jìn)行進(jìn)一步的分析。有關(guān)CVN和DWTT實(shí)驗(yàn)方面的內(nèi)容,尤其是高韌性鋼材的特性和測(cè)試結(jié)果,將在下一章中詳細(xì)討論。
上一頁
下一頁